Wafer mask alignment: Queensgate focuses on the move to 300 mm
Electronic chips are made using photolithography, which involves shining ultraviolet light through a patterned mask and onto a semiconductor wafer. The light activates a photoresist on the surface, which allows the etching of a pattern on the wafer. Through successive iterations of photolithography and the deposition of metals, devices with features as small as a few dozen nanometres are created.
Crucial to this complex manufacturing process is aligning the wafer with successive masks. This must be done in a rapid and repeatable manner, while maintaining nanometre precision throughout the manufacturing process. That’s where Queensgate – part of precision optical and mechanical instrumentation manufacturer Prior Scientific – comes into the picture.
For 45 years, UK-based Queensgate has led the way in the development of nanopositioning technologies. The firm spun out of Imperial College London in 1979 as a supplier of precision instrumentation for astronomy. Its global reputation was sealed when NASA chose Queensgate technology for use on the Space Shuttle and the International Space Station. The company has worked for over two decades with the hard-disk drive-maker Seagate to develop technologies for the rapid inspection of read/write heads during manufacture. Queensgate is also involved in a longstanding collaboration with the UK’s National Physical Laboratory (NPL) to develop nanopositioning technologies that are being used to define international standards of measurement.
Move to larger wafers
The semiconductor industry is in the process of moving from 200 mm to 300 mm wafers – which doubles the number of chips that can be produced from a wafer. Processing the larger and heavier wafers requires a new generation of equipment that can position wafers at nanometre precision.
Queensgate already works with original equipment manufacturers (OEMs) to make optical wafer-inspection systems that are used to identify defects during the processing of 300 mm wafers. Now the company has set its sights on wafer alignment systems. The move to 300 mm wafers offers the company an opportunity to contribute to the development the next-generation alignment systems – says Queensgate product manager Craig Goodman.
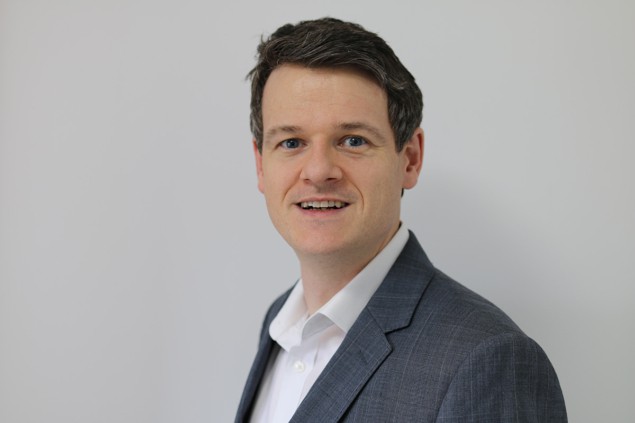
“The wafers are getting bigger, which puts a bigger strain on the positioning requirements and we’re here to help solve problems that that’s causing,” explains Goodman. “We are getting lots of inquiries from OEMs about how our technology can be used in the precision positioning of wafers used to produce next-generation high-performance semiconductor devices”.
The move to 300 mm means that fabs need to align wafers that are both larger in area and much heavier. What is more, a much heavier chuck is required to hold a 300 mm wafer during production. This leads to conflicting requirements for a positioning system. It must be accurate over shorter distances as feature sizes shrink, but also be capable of moving a much larger and much heavier wafer and chuck. Today, Queensgate’s wafer stage can handle wafers weighing up to 14 kg while achieving a spatial resolution of 1.5 nm.
Goodman explains that Queensgate’s technology is not used to make large adjustments in the relative alignment of wafer and mask – which is done by longer travel stages using technologies such as air-bearings. Instead, the firm’s nanopositioning systems are used in the final stage of alignment, moving the wafer by less than 1 mm at nanometre precision.
Eliminating noise
Achieving this precision was a huge challenge that Queensgate has overcome by focusing on the sources of noise in its nanopositioning systems. Goodman says that there are two main types of noise that must be minimized. One is external vibration, which can come from a range of environmental sources – even human voices. The other is noise in the electronics that control the nanopositioning system’s piezoelectric actuators.
Goodman explains that noise reduction is achieved through the clever design of the mechanical and electronic systems used for nanopositioning. The positioning stage, for example, must be stiff to reject vibrational noise and notch filters are used to minimize the effect of electronic noise to the sub-nanometre level.
Queensgate provides its nanopostioning technology to OEMs, who integrate it within their products – which are then sold to chipmakers. Goodman says that Queensgate works in-house with its OEM customers to ensure that the desired specifications are achieved. “A stage or a positioner for 300 mm wafers is a highly customized application of our technologies,” he explains.
While the resulting nanopositioning systems are state of the art, Goodman points out that they will be used in huge facilities that process tens of thousands of wafers per month. “It is our aim and our customer’s aim that Queensgate nanopositioning technologies will be used in the mass manufacture of chips,” says Goodman. This means that the system must be very fast to achieve high throughput. “That is why we are using piezoelectric actuators for the final micron of positioning – they are very fast and very precise.”
Today most chip manufacturing is done in Asia, but there are ongoing efforts to boost production in the US and Europe to ensure secure supplies in the future. Goodman says this trend to semiconductor independence is an important opportunity for Queensgate. “It’s a highly competitive, growing and interesting market to be a part of,” he says.
- The datasheet for Queensgate’s NPS-XYP-250Q 300 mm wafer–mask alignment stage is now available. Goodman describes it as, “the physically ‘largest’ piezo nanopositioning stage ever delivered”.
The post Wafer mask alignment: Queensgate focuses on the move to 300 mm appeared first on Physics World.