Cancer centres streamline radiotherapy workflow with SunCHECK QA platform
As the number of cancer cases continues to grow, radiation oncology departments are under increasing pressure to treat more and more patients. And as clinical facilities expand to manage this ongoing growth, and technology developments increase the complexity of radiotherapy delivery, there’s an urgent need to optimize the treatment workflow without ramping up time or staffing requirements.
To enable this level of optimization, radiation therapy departments will require an efficient quality management system that can handle both machine and patient quality assurance (QA), works seamlessly with treatment devices from multiple vendors, and provides the time savings required to ease staff workload.
Driven by growth
A case in point is the Moffitt Cancer Center in Florida, which in 2018 shifted all of its QA to SunCHECK, a quality management platform from Sun Nuclear that combines hardware and software to streamline treatment and delivery system QA into one centralized platform. Speaking at a recent Sun Nuclear webinar, clinical physicist Daniel Opp explained that the primary driver for this switch was growth.
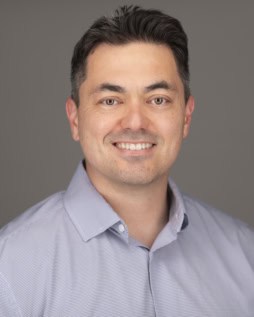
“In 2018, our physicians were shifting to perform a lot more SBRT [stereotactic body radiation therapy]. Our leadership had plans in motion to add online adaptive planning as well as expand with opening more radiation oncology centres,” he explained.
At that time, the centre was using multiple software platforms and many different imaging phantoms to run its QA, with physicists still relying on manual measurements and qualitative visual assessments. Now, the team performs all machine QA using SunCHECK Machine and almost all patient-specific QA [PSQA] using SunCHECK Patient.
“Our QA software and data were fractured and all over the place,” said Opp. “The move to SunCHECK made sense as it gave us the ability to integrate all measurements, software and databases into a one-stop shop, providing significant time savings and far cleaner record keeping.”
SunCHECK also simplifies QA procedures by consolidating tests. Opp explained that back in 2018, photon tests on the centre’s linacs required five setups, 12 measurements and manually entering values 22 times; SunCHECK reduced this to one setup, four measurements and no manual entries. “This alone gives you an overview of the significant time savings,” he said.
Another benefit is the ability to automate tests and ensure standardization. “If you tell our large group of physicists to do a picket fence test, we’ll all do it a little differently,” Opp explained. “Having one system on which we’re all running the same tests means that we’re able to do the test in the same way across all our linacs.”
Opp noted that SunCHECK displays all required information on an easy-to-read screen, with the patient QA worklist on one side and the machine QA worklist on the other. “You see a snapshot of the clinic and can figure out if there’s anything you need to take care of. It’s very efficient in letting you know when something needs your attention,” he said.
A unified platform
Medical physicist Patricia Sansourekidou of the University of New Mexico (UNM) Comprehensive Cancer Center in Albuquerque, also implemented SunCHECK to improve the efficiency of the site’s quality management programmes.
Sansourekidou initiated the switch to SunCHECK after joining UNM in 2020 as its new director of medical physics. At that time the cancer centre was treating about 1000 patients per year. But high patient numbers led to a long waiting list – with roughly three months between referral and the start of treatment – and clear need for the facility to expand.
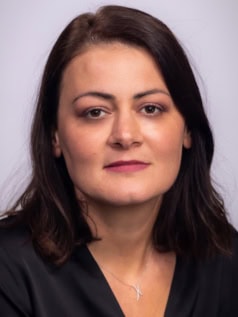
Assessing the centre’s QA procedures in 2020 revealed that the team was using a wide variety of QA software, making routine checks time consuming. Monthly linac QA, for example, required roughly 32 files and took about 14 hours to perform. In addition, Sansourekidou noted, physicists were spending hours every month adjusting the machines. “One day it was the energy that was off and then the output was off; I soon realised that, in the absence of appropriate software, we were making adjustments back and forth,” she said. “More importantly, we had no way to track these trends.”
Sansourekidou concluded that the centre needed an improved QA solution based on one unified platform. “So we went on a physics hunt,” she said. “We met with every vendor out there and Sun Nuclear won the request for proposal. So we implemented SunCHECK Machine and SunCHECK Patient.”
Switching to SunCHECK reduced monthly QA to just 4–5 hours per linac. “We’re saving about nine hours per linac per month; that’s 324 hours per year when we could be doing something else for our patients,” said Sansourekidou. Importantly, the new software enables the team to visualize trends and assess whether a genuine problem is present.
For daily QA, which previously required numerous spreadsheets and systems, SunCHECK’s daily QA template provides time savings of about 60%. “At six in the morning, that’s important,” Sansourekidou pointed out. Annual QA saw roughly 33% time savings, while for the 70% of patients requiring PSQA, time savings were about 25%.
Another “unexpected side effect” of deploying SunCHECK, said Sansourekidou, is that the IT department was happy to maintain one platform. “Every time we have a new physicist, it’s much easier for our IT department to set them up. That has been a huge benefit for us,” she said. “Additionally, our service engineers are happy because we are not spending hours of their time adjusting the machine back and forth.”
“Overall, I thought there were great improvements that really helped us justify the initial investment – not just monetary, but also time investment from our physics team,” she said.
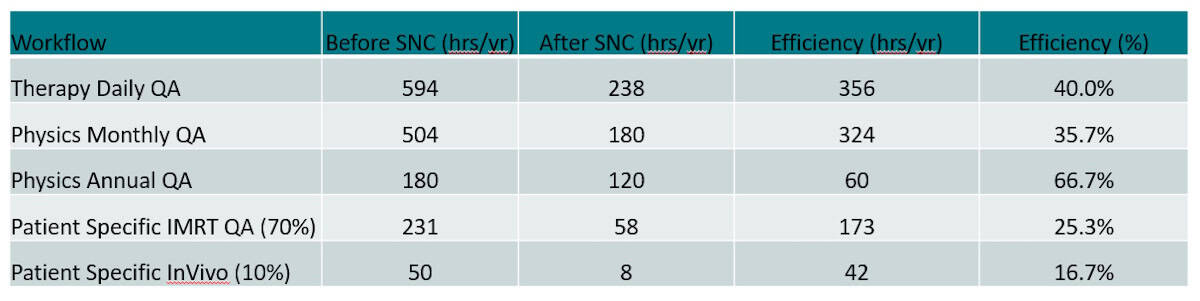
Phantom-free QA
For Opp, one of the biggest features enabled by SunCHECK was the move to phantom-free PSQA, which saves a lot of time and eliminates errors that can be inherent to phantom-based QA. In the last year, the Moffitt team also switched to using DoseCHECK – SunCHECK’s secondary 3D dose calculation algorithm – as the foundation of its quality checks. Alongside, a RayStation script checks plan deliverability to ensure that no problems arise once the patient is on the table.
“We don’t do our pre-treatment QA anymore. We rely on those two to get confidence into the final work and then we run our logs off the first patient fraction,” Opp explained. “We have a large physics group and there was natural apprehension, but everybody got on board and agreed that this was a shift we needed to make. We leveraged DoseCHECK to create a better QA system for ourselves.”
Since 2018, both patient workload and staff numbers at the Moffitt Cancer Center have doubled. By the end of 2025, it will also have almost doubled its number of treatment units. The centre has over 100 SunCHECK users – including therapists, dosimetrists and physicists – and Opp emphasized that the system is robust enough to handle all these users doing different tasks at different times without any issues.
As patient numbers increase, the time savings conferred by SunCHECK help reduce staff workload and improve quality-of-life for users. The centre currently performs about 100 PSQA procedures per week, which would have taken about 37 hours using previous QA processes – a workload that Opp notes would not be managed well. SunCHECK reduced the weekly average to around seven hours.
Similarly, linac QA previously required two or three late nights per month (or one full day on the weekend). “After the switch to SunCHECK, everybody’s pretty much able to get it done in one late night per month,” said Opp. He added that the Moffitt Cancer Center’s continuing growth has required the onboarding of many new physicists – and that it’s significantly easier to train these new staff with all of the QA software in one centralized platform.
Enabling accreditation
Finally, accreditation is essential for radiation oncology departments to demonstrate the ability to deliver safe, high-quality care. The UNM Comprehensive Cancer Centre’s previous American College of Radiology (ACR) accreditation had expired before Sansourekidou’s arrival, and she was keen to rectify this situation. And in March 2024 the centre achieved ASTRO’s APEx accreditation.
“SunCHECK helped with that,” she said. “It wasn’t the only reason, there were other things that we had to improve, but we did come across as having a strong physics programme.”
Achieving accreditation also helps justify the purchase of a totally new QA platform, Sansourekidou explained. “The most important thing to explain to your administration is that if we don’t do things the way that our regulatory bodies advise, then not only will we lose our accreditation, but we will fall behind,” she said.
Sansourekidou emphasized that the efficiency gains conferred by SunCHECK were invaluable for the physics team, particularly for out-of-hours working. “We saw huge time savings for both monthly and daily QA,” she said. “It is a large investment, but improving efficiency through investment in software will really help the department in the long term.”
The post Cancer centres streamline radiotherapy workflow with SunCHECK QA platform appeared first on Physics World.