Bank of America: US-Made iPhones Would Face 90% Cost Surge
Moving iPhone production from China to the United States could increase manufacturing costs by up to 90%, analysts at Bank of America warned on Wednesday (via Bloomberg).
According to BofA analysts led by Wamsi Mohan, shifting iPhone assembly to America is technically possible, however it would dramatically increase production expenses and create logistical complications.
"iPhone cost can increase 25% purely on higher labor cost in the U.S.," the analysts wrote in a note to clients. They explained that even if Apple finds domestic workers for final assembly, a "significant portion" of iPhone components would still need to be manufactured in China and imported to the States.
Assuming Apple faces reciprocal tariffs on those imported components, the total manufacturing cost could rise by 90% or more, the analysts estimated.
The analysis follows statements from President Trump earlier this week calling Apple's manufacturing in China "unsustainable." According to White House press secretary Karoline Leavitt, Trump "absolutely" believes Apple could manufacture iPhones in the United States. During a recent media briefing, Leavitt said the President believes "we have the labor, we have the workforce, we have the resources to do it."
Trump's aggressive trade policies singled out China on Wednesday, pausing reciprocal tariffs on many countries for 90 days but increasing duties on Chinese imports to 125%. In response, China has imposed 84% retaliatory levies on American goods. It's becoming increasingly difficult to assess where the stand-off goes from here.
Uncertainty caused by the trade war has battered Apple's stock, which has fallen 14% since Trump's April 2 tariff announcement, erasing approximately $479 billion in market capitalization. Despite a recent 10% rebound, Apple shares remain down 23% year-to-date.
For Apple to make U.S. assembly economically viable, Mohan suggests the company would need tariff waivers on components and subassemblies manufactured outside the country. However, he doesn't believe this is likely to happen.
"Unless it becomes clear as to how permanent the new tariffs are, we do not expect Apple to take the step of moving manufacturing into the U.S.," Mohan stated. Instead, he anticipates Apple will "continue to diversify its supply chain, and also increase production of iPhones in other countries such as India."
Apple has not officially commented on how it plans to address the current tariff situation. Apple will need to pay the 125% tariff on all goods coming to the United States from China, but it can import devices from other countries like India, Taiwan, and Vietnam at the lower 10% rate.
This article, "Bank of America: US-Made iPhones Would Face 90% Cost Surge" first appeared on MacRumors.com
Discuss this article in our forums
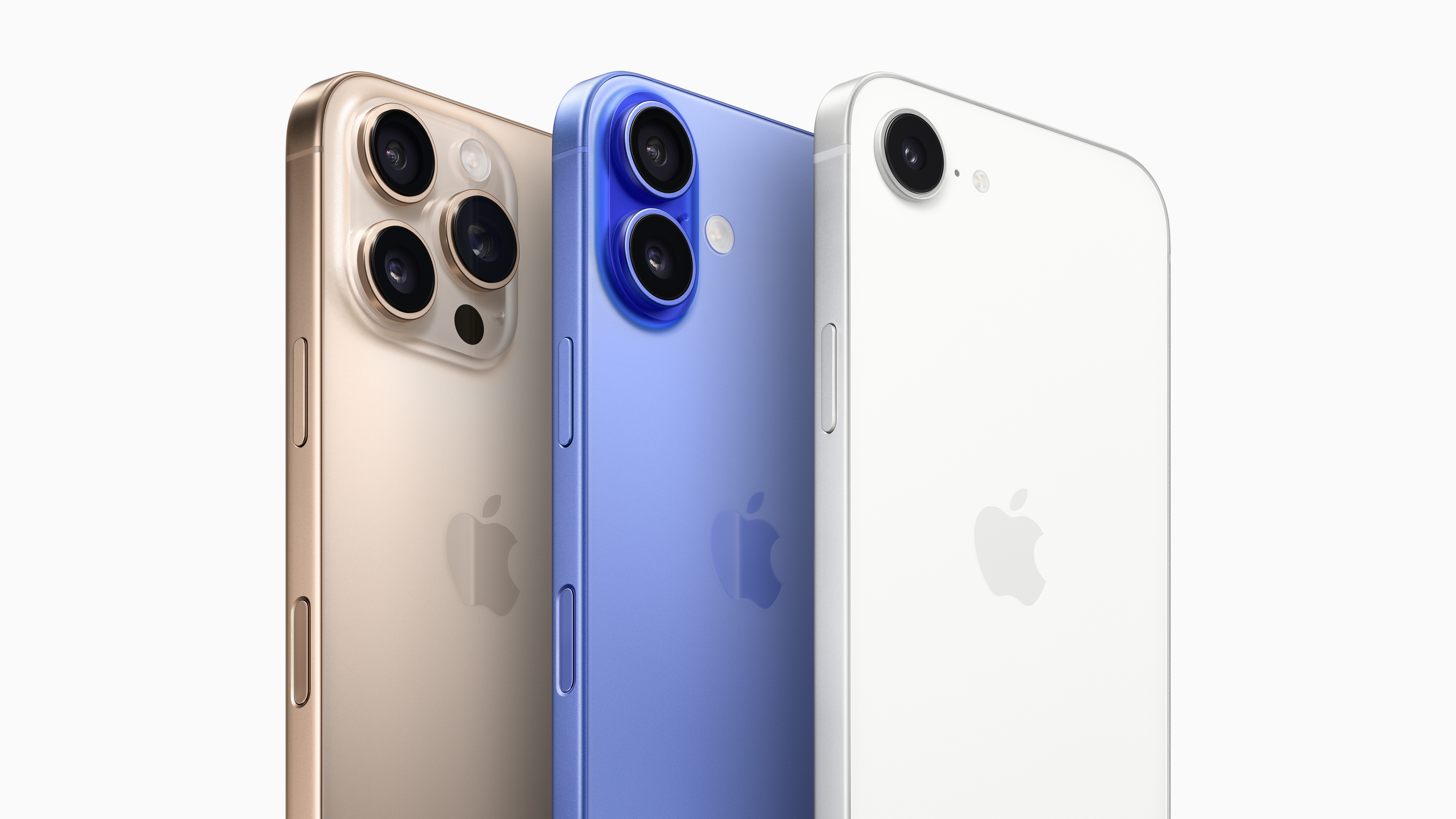
According to BofA analysts led by Wamsi Mohan, shifting iPhone assembly to America is technically possible, however it would dramatically increase production expenses and create logistical complications.
"iPhone cost can increase 25% purely on higher labor cost in the U.S.," the analysts wrote in a note to clients. They explained that even if Apple finds domestic workers for final assembly, a "significant portion" of iPhone components would still need to be manufactured in China and imported to the States.
Assuming Apple faces reciprocal tariffs on those imported components, the total manufacturing cost could rise by 90% or more, the analysts estimated.
The analysis follows statements from President Trump earlier this week calling Apple's manufacturing in China "unsustainable." According to White House press secretary Karoline Leavitt, Trump "absolutely" believes Apple could manufacture iPhones in the United States. During a recent media briefing, Leavitt said the President believes "we have the labor, we have the workforce, we have the resources to do it."
Trump's aggressive trade policies singled out China on Wednesday, pausing reciprocal tariffs on many countries for 90 days but increasing duties on Chinese imports to 125%. In response, China has imposed 84% retaliatory levies on American goods. It's becoming increasingly difficult to assess where the stand-off goes from here.
Uncertainty caused by the trade war has battered Apple's stock, which has fallen 14% since Trump's April 2 tariff announcement, erasing approximately $479 billion in market capitalization. Despite a recent 10% rebound, Apple shares remain down 23% year-to-date.
For Apple to make U.S. assembly economically viable, Mohan suggests the company would need tariff waivers on components and subassemblies manufactured outside the country. However, he doesn't believe this is likely to happen.
"Unless it becomes clear as to how permanent the new tariffs are, we do not expect Apple to take the step of moving manufacturing into the U.S.," Mohan stated. Instead, he anticipates Apple will "continue to diversify its supply chain, and also increase production of iPhones in other countries such as India."
Apple has not officially commented on how it plans to address the current tariff situation. Apple will need to pay the 125% tariff on all goods coming to the United States from China, but it can import devices from other countries like India, Taiwan, and Vietnam at the lower 10% rate.
This article, "Bank of America: US-Made iPhones Would Face 90% Cost Surge" first appeared on MacRumors.com
Discuss this article in our forums